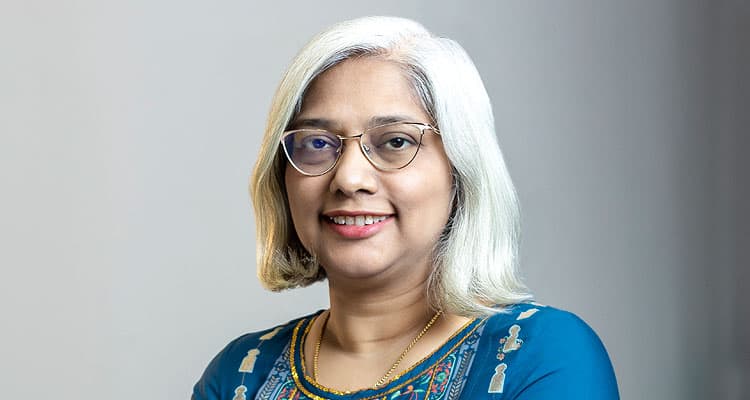
The Indian pharma industry, long hailed as a global powerhouse, finds itself at a crossroads. Once a beacon of growth and profitability, the sector is now grappling with a complex web of challenges that are eroding margins and inflating overheads.
Pressure on margins: A reality check for India Pharma
In recent years, Indian pharmaceutical companies have seen a substantial decline in profitability, dropping by approximately 20-30 per cent over the past six to eight years, aside from a brief surge during the pandemic. This decline is primarily driven by the ongoing price erosion in the US market, the chief destination for Indian generics. Intensified competition and the consolidation of distributors in the US have increased their bargaining power, exerting downward pressure on prices and compressing profit margins for Indian pharmaceutical firms.
The decline has led many pharma companies to aggressive cost-cutting, including reducing QA/QC staff, cutting R&D investment, and throttling raw materials. Some of these short-term fixes, often driven by trying to achieve industry benchmarks, often harm long-term capacity and adaptability to market changes. This is especially important since the signals from the export markets are not uniform. While the general trend may be a price decline in most drugs, there are frequent windows of opportunity that open up, for example due to supply shortages. Without agility, companies cannot respond and take advantage of these opportunities.
However, if organisations need to have both agility and low-cost operations to sustain profitability, it is essential to move beyond current methodologies and adopt innovative strategies. And the path lies in achieving operational excellence while maintaining high resource productivity. This transformation must encompass a strategic overhaul in pharma operations, including 1) manufacturing, 2) quality assurance and control (QA/QC), and 3) research and development (R&D).
1) Operational excellence: The new imperative
Many pharma plants struggle with very little room for flexibility in operations in this environment wherein processes are under stringent regulatory control. Resultant, extended lead times, typically ranging from six to nine months, hinder prompt responses to market demand fluctuations, often resulting in excessive inventory or costly expedited processes. For instance, while the desired inventory level is two to three months, the average finished goods (FG) inventory in US warehouses of Indian pharma companies is around five to six months of sales. Emergency air shipments — costing one to two per cent of sales — further strain resources.
ing away from forecast-based procurement is crucial. Traditional methods often lead to unreliable production plans and inventory issues, exacerbated by frequent forecast revisions. Adopting a ‘pull’ based system with daily replenishment signals from strategic buffers can improve agility and efficiency in pharma manufacturing, reducing lead times by 25-50 per cent and inventory levels by 20-40 per cent.
Secondly, it is necessary to reevaluate current finite scheduling methods that tend to optimise multiple work centres by scheduling each one back-to-back. This approach ignores the system’s inherent variability, which can jeopardise production at the actual bottleneck—the point that controls the plant’s output. Instead, the focus should be on generating a finite schedule specifically for the identified bottleneck while allowing other work centres to operate with adequate time buffers.
Material flow on the shop floor should not be controlled according to a fixed schedule in many non-constrained work centres. This will ensure that constraint machines are never starved while the system’s work-in-progress (WIP) is minimal. This approach allows for dynamic adjustments to production plans, enhancing capacity utilisation of pharma plants and reducing airfreight costs by over 75 per cent.
Lastly, enhancing visibility and integration with API suppliers is vital. Companies should integrate supply chain planning with both internal units and outsourced API partners to eliminate inefficiencies, such as excess inventory and wastage. This strategic integration can lead to a 20-40 per cent reduction in inventory and substantial cost savings.
2) Quality control: A balancing act
Maintaining quality systems in the highly regulated US market is expensive, but failing to meet standards can be even costlier. Companies facing FDA 483s understand the severe consequences of lapses in GMP or GLP processes. To prevent such issues, Indian firms must transition from ‘Inspection Readiness’ to ‘Perpetual Regulatory Readiness.’ This shift ensures that FDA inspections become routine, not disruptive. Firms should enhance their root cause analysis (RCA) capabilities for all quality incidents, aiming to reduce invalid OOS by over 70 per cent and lab incidents by 50-70 per cent.
3) R&D efficiency: Maximising output
Many generic pharma R&D projects try to align closely with patent expiries to maximise launch value since delays can worsen price erosion and render a drug unviable due to high costs, including regulatory fees and bioequivalence studies. To avoid this, companies often start R&D projects early. Yet, shared resources and the iterative nature of work lead to system overload, with many firms working on project pipelines that exceed capacity by 60-100 per cent. This results in slow project progress, delayed department responses, and procurement issues. Transitioning to project flow management, with clear capacity definitions and agile planning, can improve performance significantly, reducing lead times by 30-50 per cent and increasing project output by 50 per cent.
Embracing innovation for sustainable growth
The Indian pharma industry stands at a pivotal juncture, where traditional practices can no longer guarantee sustained success. As profitability declines and operational challenges intensify, the path forward is clear: embracing innovation and operational excellence is not just an option— it’s a necessity. By rethinking manufacturing processes, enhancing quality control measures, and optimising R&D efficiency, Indian pharma companies can not only navigate the turbulent landscape but also secure their place as global leaders.
The post appeared first on .