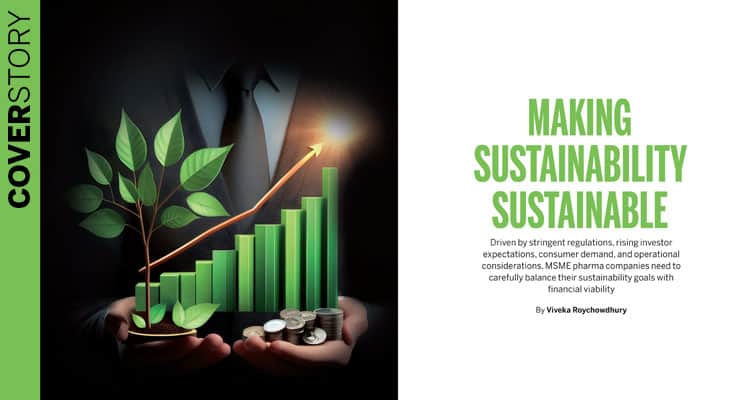
Prime Minister Narendra Modi’s mention of ‘green jobs’ in his Independence Day speech this year re-emphasised his commitment to achieving the Net Zero emissions target by 2070. The question is how will India, arguably the world’s third-largest greenhouse gas emitter, achieve this target, with even the goal of limiting global warming to an increase of no more than 1.5 degrees Celsius (1.5°C) above pre-industrial levels, looking like a steep challenge?
As the market regulator, the Securities and Exchange Board of India (SEBI) has added heft to the net zero target, by expanding the disclosures that listed entities need to make related to Environmental, Social and Governance (ESG) factors. A SEBI circular dated July 12, 2023 mandates that the top 150 listed entities (by market cap) had to undertake reasonable assurance of Business Responsibility and Sustainability Reporting (BRSR) Core from FY23-24, and this will extend to the top 1000 listed entities by FY26-27. The circular also requires the top 250 listed companies by market cap to disclose BRSR Core information for their value chain in their Annual Reports for FY24-25 on a comply-or-explain basis.
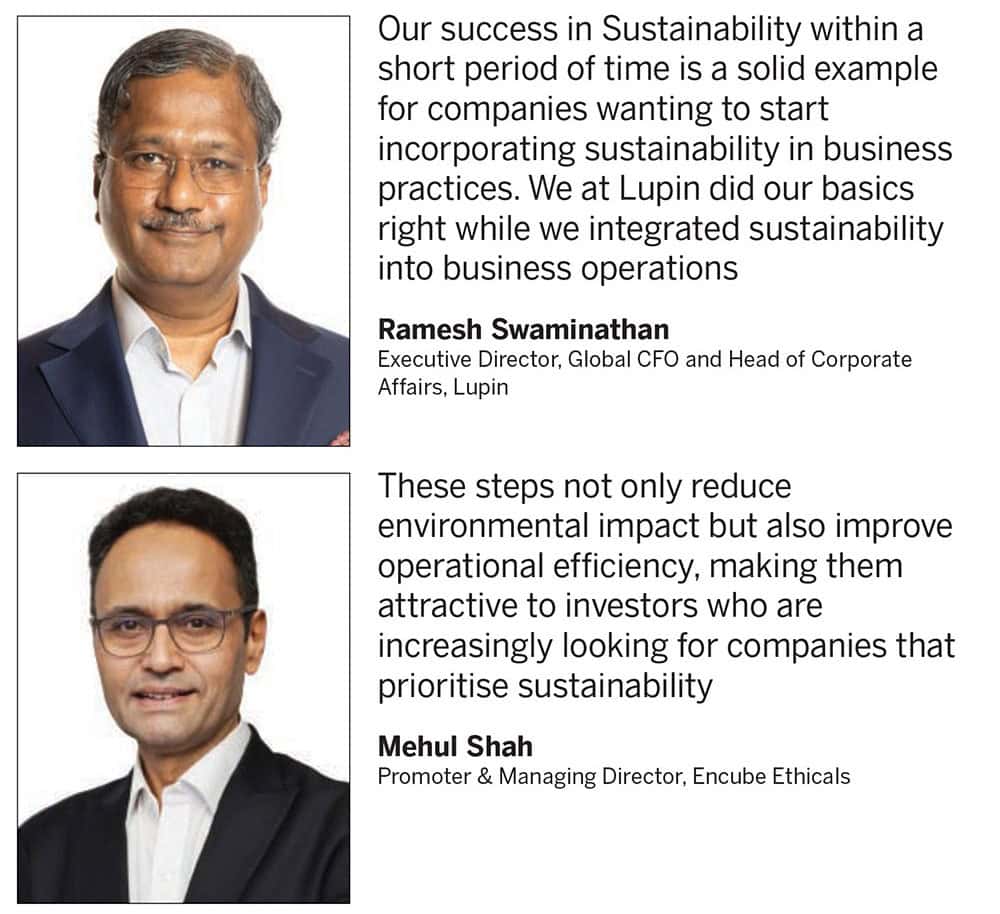
As Ramesh Swaminathan, Executive Director, Global CFO and Head of Corporate Affairs, Lupin points out, the pharma industry’s contribution to the climate crisis comes from its 4.4 per cent share of global CO2 emissions. Although this percentage is lower than that of other industries, without action, emissions are expected to rise. Thus, he points out that the pharma industry has a unique responsibility to take action and promote sustainability. While it needs to reduce its greenhouse gas (GHG) emissions through net-zero strategies, it also needs to address the adverse health effects of the climate crisis by providing affordable medicines. Listed pharma companies in India have been reporting on their ESG initiatives for the past few years.
Quoting from the EY-CII 2024 report ‘How can Sustainability and ESG be the microscope and telescope in the Indian healthcare sector? Nitesh Mehrotra, Partner, ESG & Sustainability, EY India highlights increasing allocations towards environmental and social initiatives within research and development (R&D) and capital expenditure (capex). 21 per cent of spending is dedicated to environmental and social activities in R&D, showcasing a commitment to innovation and sustainable practices. Equally noteworthy is the allocation of 13 per cent of spending towards environmental and social initiatives within capex, affirming a strategic commitment to infrastructure and operational enhancements for bolstering sustainability performance.
Toeing the green line
Larger pharma companies are toeing the SEBI line and are also prominent on global ESG ratings. In December 2023, Dr Reddy’s Laboratories became the first Indian pharma company to earn a place in the Standard & Poor Dow Jones Sustainability World Index (DJSI World) for 2023. Alongside its debut in DJSI World, the company retained its place in the Dow Jones Sustainability Index for Emerging Markets (DJSI EM) for the eighth year in a row. Dr Reddy’s scored 77/100 in the 2023 S&P Global CSA, achieving full scores in Innovation Management, Impact on Access to Healthcare, Climate Risk Management, and Resource Efficiency and Circularity. The company ranked in the top decile percentile and achieved the sixth-highest score out of 347 companies assessed in the pharma industry in the S&P Global
CSA. Dr Reddy’s S&P Global ESG score, measuring the company’s performance on and management of material ESG risks, opportunities and impact, is 78/ 100. Dr Reddy’s has been awarded ‘Gold Medal’ status by EcoVadis, the global sustainability ratings agency, for its score of 70/100 in its 2023 scorecard.
A Dr Reddy’s spokesperson’s statement also informed that in 2022, the company’s largest formulations manufacturing facility in Bachupally joined the Global Lighthouse Network (GLN) of the World Economic Forum – a community of over 100 manufacturers that are showing leadership in applying Fourth Industrial Revolution (Industry 4.0 or 4IR) technologies to drive impact in productivity, workforce engagement, sustainability and supply chain resilience. In addition, five of the company’s manufacturing facilities are certified under the Indian Green Building Council (IGBC). In FY2024, the company evaluated 26 products through chemistry gate clearance. Through the implementation of 17 cost-improvement projects leveraging green chemistry principles, Dr Reddy’s successfully reduced nearly 22 per cent hazardous waste generation in the manufacturing of those products.
Lupin embarked on their sustainability journey four years ago, and made an entry in the S&P Global Sustainability Yearbook 2024, with a notable Corporate Sustainability Assessment (CSA) score of 65/100, and an S&P Global ESG Score of 69. Sun Pharma’s CSA and ESG scores were both 68, Cipla’s CSA was 67, ESG 70, and Neuland Laboratories had a CSA score of 60 and ESG score of 64. Similarly, Biocon’s S&P Global CSA score was 61, and ESG score was 63, placing it among the Top 10 global biotech companies.
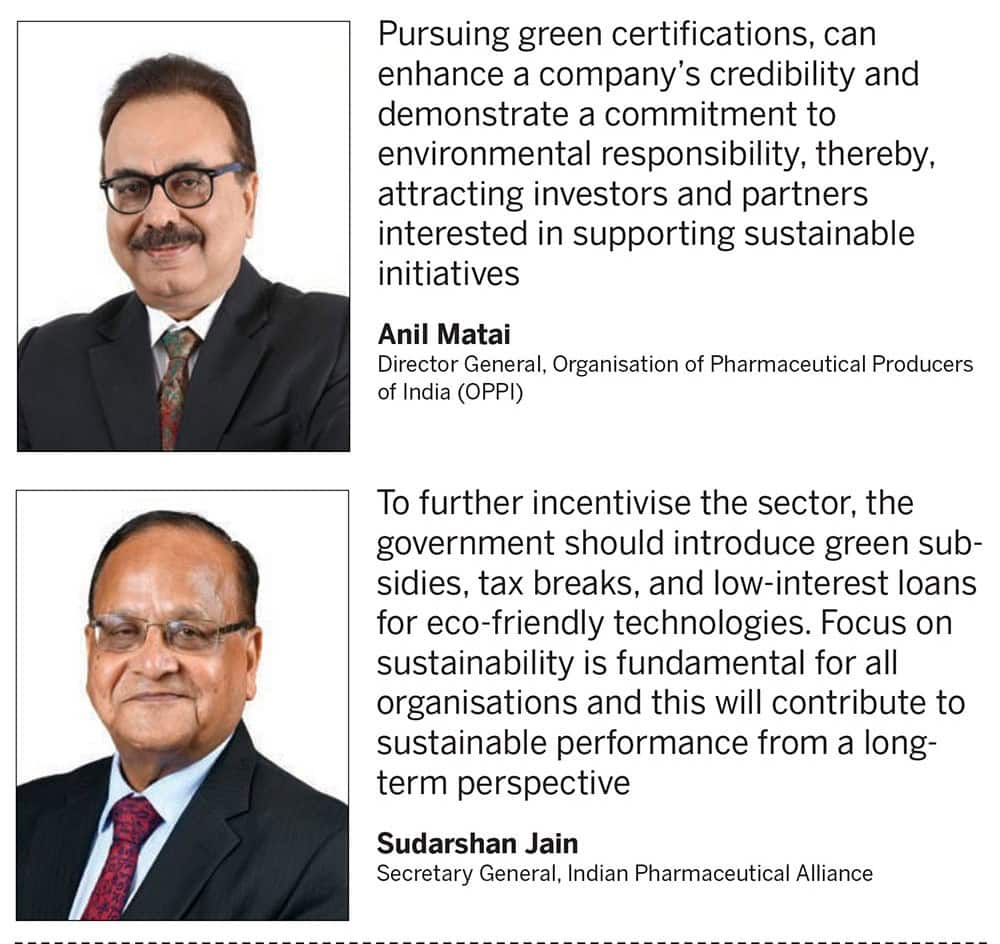
Sudarshan Jain, Secretary General, Indian Pharmaceutical Alliance, which represents large Indian pharma companies, summed up this evolution, saying, “Sustainability is a strategic priority for pharma companies as the sector involves a significant environmental footprint. IPA members are advancing green practices including sustainable supply chains, efficient technologies, carbon neutrality, waste management, and energy and water conservation practices. Financial sustainability, achieved by integrating ESG principles, ensures long-term stability and growth.”
Anil Matai, Director General, Organisation of Pharmaceutical Producers of India (OPPI), which represents India subsidiaries of MNC pharma companies, believes that true sustainability involves adopting a long-term perspective that prioritises the well-being of both the people and the planet. This entails a dedication to social, environmental, and civic responsibilities that go well beyond immediate gains. OPPI’s publication titled, Putting the Country First Taking the Country Far, lists the efforts of OPPI member companies.
As an ESG consultant, Sunil Kumar, Director, SIPL also concurs that the pharma sector is increasingly making investments in sustainability, driven by a combination of regulatory pressures (for instance, regulations like the European Union’s Green Deal and the US Securities and Exchange Commission’s ESG disclosure requirements are becoming more stringent), investor expectations, consumer demand, and operational considerations.
With +20 clients in the pharma and related intermediate sectors, SIPL has conducted life cycle Assessments (LCAs), and provided ESG solutions and SimaPro software to pharma majors like Novartis, Sun Pharma, Biocon, Ajanta Pharma, Dorf Ketal, Gharda Chemicals, Cardolite Specialty Chemicals, Anupam Rasayan India, SRF, etc.
Giving the equipment manufacturer’s point of view, Shivshankar SR, CEO, ACG Packaging Materials, reiterates that it is important for organisations to proactively set targets and focus on long-term initiatives that will provide value realisation and business transformation towards creating a more sustainable and resilient future. He mentions that within ACG’s business, their adherence to the Science Based Targets initiative (SBTi) through their recently announced strategic partnership with EY Parthenon, underscores their commitment to conscientious corporate stewardship.
Summing up, Shivshankar of ACG Packaging reminds us that the mission to reduce the overall carbon footprint remains a driving principle for the pharma sector, with a focus on making manufacturing ‘contained, continuous and connected’ – optimising raw material use and reducing waste. Shivshankar singles out large-scale manufacturers who must expedite net zero objectives, thereby effectuating a meaningful reduction in their carbon emissions. While he concedes that embarking on the journey towards decarbonising entire processes will undoubtedly prove overwhelming for many, he reminds us that “ultimately it’s about looking towards the future and trying to understand wide-ranging stakeholder needs to create long-term and effective solutions.”
MSME pharma sustainability path
But MSME pharma companies are also a huge part of India Pharma Inc. According to the Confederation of Indian Industries (CII), there are around 8,000 small and medium enterprises (SME) units, accounting for about 70 per cent of the total number of the pharma units in India. Forward looking mid size pharma companies have already committed to ESG goals realising that there are multiple benefits beyond compliance. As Mehul Shah, Promoter & Managing Director, Encube Ethicals puts it, “Sustainability is more than a commitment, it’s a path to operational efficiency and long-term value creation.”( . expresspharma.in/sustainabilityis-more-than-a-commitment-itsa-path-to-operational-efficiencyand-long-term-value-creation/)
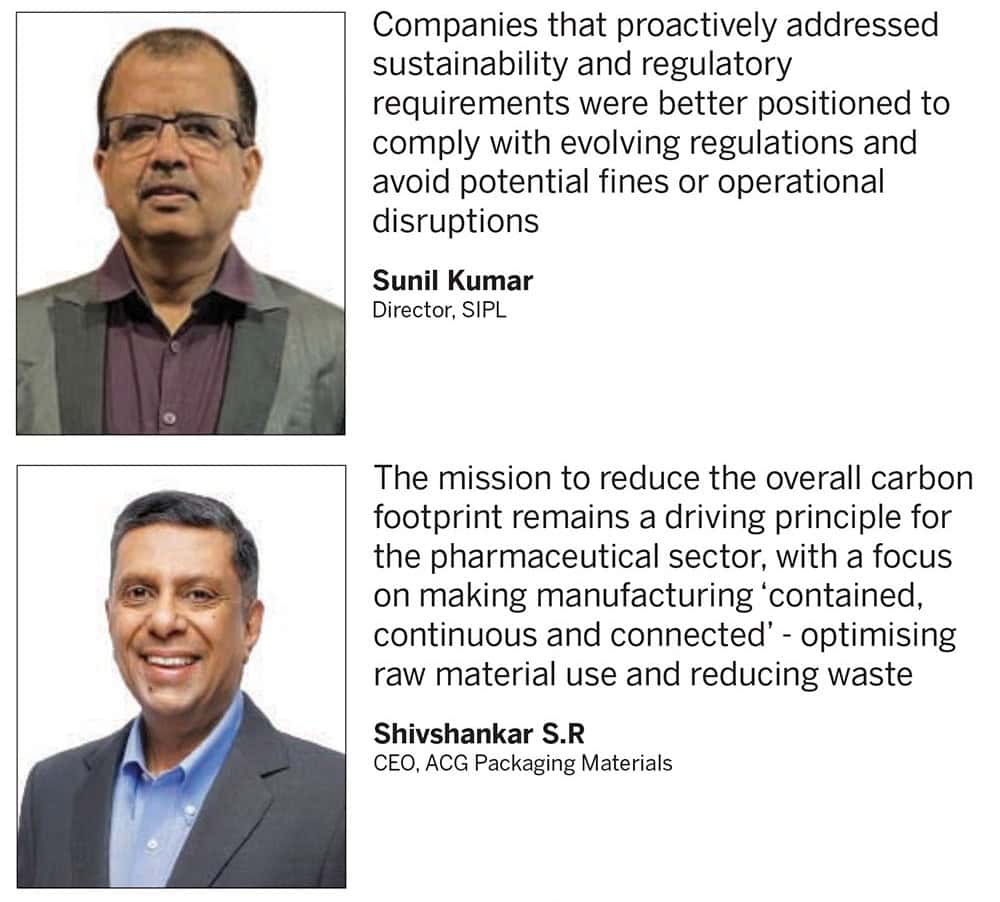
Summarising the challenges, Shah points out that with growing awareness of the environmental impact of pharma manufacturing, such as pollution from toxic discharges, pharma companies face the challenge of balancing their sustainability goals with the economic pressures of operating in a highly regulated environment. One of the primary challenges the industry faces is the inherent resource intensity of pharma manufacturing. The production of drugs requires significant amounts of water, energy, and raw materials, which contribute to a substantial carbon footprint. Furthermore, the management of pharma waste, especially active pharma ingredients (APIs), poses significant environmental risks if not handled responsibly. The complexity of global supply chains adds another layer of difficulty in ensuring that sustainability is maintained at every stage of production, explains Shah.
Drawing on his experience as an ESG consultant, Sunil Kumar comments that the sustainability journey for pharmaceutical companies, including smaller and MSME pharma clients, has varied widely depending on their size, resources, and initial practices. However, there are common outcomes and best practices that can guide MSME and smaller pharma companies in their sustainability efforts.
Enumerating some best practices, Sunil Kumar says that for MSME and smaller pharma companies, the way forward involves integrating sustainability into core business strategies and operations. “By starting with manageable changes, leveraging support, setting goals, and fostering a culture of continuous improvement, these companies can achieve significant benefits and contribute positively to environmental and social outcomes. As the industry evolves, ongoing adaptation and commitment to sustainability will be key to long-term success and resilience.”
First green steps
Enumerating the early steps that MSME pharma companies can consider as they could result in quick gains to encourage more investments in sustainable manufacturing practices, Shah suggests that before making any major changes, the first step should be to optimise what the company has. Operations can become sustainable if companies can enhance the lifespan and performance of machinery, reduce downtime and minimise resource use. This evaluation helps identify areas where simple optimisations can lead to significant improvements.
For instance, companies can start by improving energy efficiency and result in immediate reductions in energy consumption and costs. Implementing water conservation techniques, such as low-flow fixtures or rainwater harvesting, can reduce water consumption quickly. Companies can also explore the reuse of treated wastewater for non-critical operations like cleaning or cooling systems. Shah reasons that these steps not only reduce environmental impact but also improve operational efficiency, making them attractive to investors who are increasingly looking for companies that prioritise sustainability.
He also singles out ‘green financing’ as another popular avenue for quick gains in sustainability. Simply put, this is a type of loan designed to promote environmentally friendly activities, encouraging companies to invest in projects that reduce their environmental impact. These loans come with reduced interest rates, providing financial incentives for companies to meet their sustainability goals.
For example, Shah points out that Biocon’s $1.2 billion green loan to fund its purchase of Viatris’ biosimilars business last year, was one of the largest green loans raised by a pharma company in the APAC region. The company agreed to meet certain sustainability targets that helped reduce the cost of the loan.
As EY India’s Mehrotra explains, “Transparent reporting of ESG metrics not only enhances investor confidence but also serves as a barometer of a company’s resilience and adaptability in a rapidly evolving world. Integrating ESG into investment strategies not only aligns with ethical imperatives but also unlocks opportunities for sustainable growth.”
Adding to the suggestions, OPPI’s Matai advocates that educating and training employees on sustainable practices fosters a culture of sustainability within the organisation, which can have a ripple effect on overall operations. From the investability angle, he agrees that “Pursuing green certifications, can enhance a company’s credibility and demonstrate a commitment to environmental responsibility, thereby, attracting investors and partners interested in supporting sustainable initiatives.”
Sayooj Thekkevariath, Partner, Climate Change and Sustainability Services at EY India goes further, stating that to make sustainability truly sustainable in pharma, a holistic approach is essential. This involves adopting circular economy principles like recycling, reusing, and recovering materials which can significantly reduce waste and resource consumption. It also involves leveraging digital technologies for process optimisation, supply chain visibility, and energy management which can enhance efficiency and reduce environmental impact.
Similarly, collaborative partnerships with suppliers, academia, and industry peers can accelerate innovation and knowledge sharing whereas risk management, involving identifying and mitigating environmental risks can prevent costly disruptions and enhance resilience. However, Thekkevariath cautions that companies need to consider a long-term perspective, as viewing sustainability as a long-term investment rather than a cost can drive strategic decision-making. In terms of early steps leading to quick gains, Thekkevariath opines that to incentivise early investments, the industry can focus on energy efficiency, waste reduction, water conservation and employee engagement.
Lupin’s sustainability story
Swaminathan offers Lupin as an example of achieving success in sustainability within a short period of time. Lupin’s mantra: get the basics right while integrating sustainability into business operations. Swaminathan touches on five aspects of this journey. Firstly, integrating sustainability into the core business strategy, “ensuring the integration of sustainability practices into the very fabric of our strategy and this accelerated our journey towards becoming a patient-centric sustainability organisation.” Secondly, Lupin divided the goals into two pillars: aspirational short term ESG SMART goals and long-term Perpetual Commitments. Swaminathan explains that ESG SMART goals have specific targets and timelines, which are monitored every quarter, whereas the Perpetual Commitments represent the company’s ongoing efforts to improve, track, and report monthly progress.
Thirdly, Lupin links executive pay to ESG goals, with all president-level personnel having ESG goals as their individual goals. Next, taking this down the line, the company integrates sustainability with employees, where every individual thrives and is valued and empowered to contribute to the business ESG goals. And fifthly, Lupin involves their supply chain partners, actively engaging with suppliers, partners, and stakeholders to ensure their environmental and social objectives are shared in pursuance of Lupin’s ESG goals.
Sharing a few outcomes of this sustainability strategy, Swaminathan mentions that Lupin’s share of renewable fuel in the energy mix increased by four times, contributing to 33.8 per cent of total energy derived from fuel sources in FY24. The company achieved a 21 per cent reduction in Scope 1 & 2 emissions from the previous year. Looking forward, the company has successfully committed and joined the “Science Based Target Initiatives” which will drive progress towards decarbonisation of the value chain.
On the water stewardship status, in FY24, 44 per cent of total water withdrawn at Lupin facilities was recycled, and the company’s target is to achieve 50 per cent by 2025. Giving an example of Lupin’s green chemistry skills, Swaminathan explains how the manufacturing of a particular antiviral molecule previously involved a three-step process, which delivered an overall yield of 0.91 per cent with an e-factor of 88 and an atom economy of 35 per cent. Lupin transitioned into a single-step process, delivering a yield of 1.4 per cent along with an E-factor improvement of 90 per cent and an atom economy improvement of 58 per cent.
Why continuous manufacturing is more sustainable…
Pharma companies in India are in a transition phase, as they explore more sustainable manufacturing concepts. However, cost remains a key consideration. Equipment makers however argue that while the initial cost to switch to more sustainable options does involve considerable capex, the long-term savings more than make up. Thus advocating short-term pain for long-term gain.
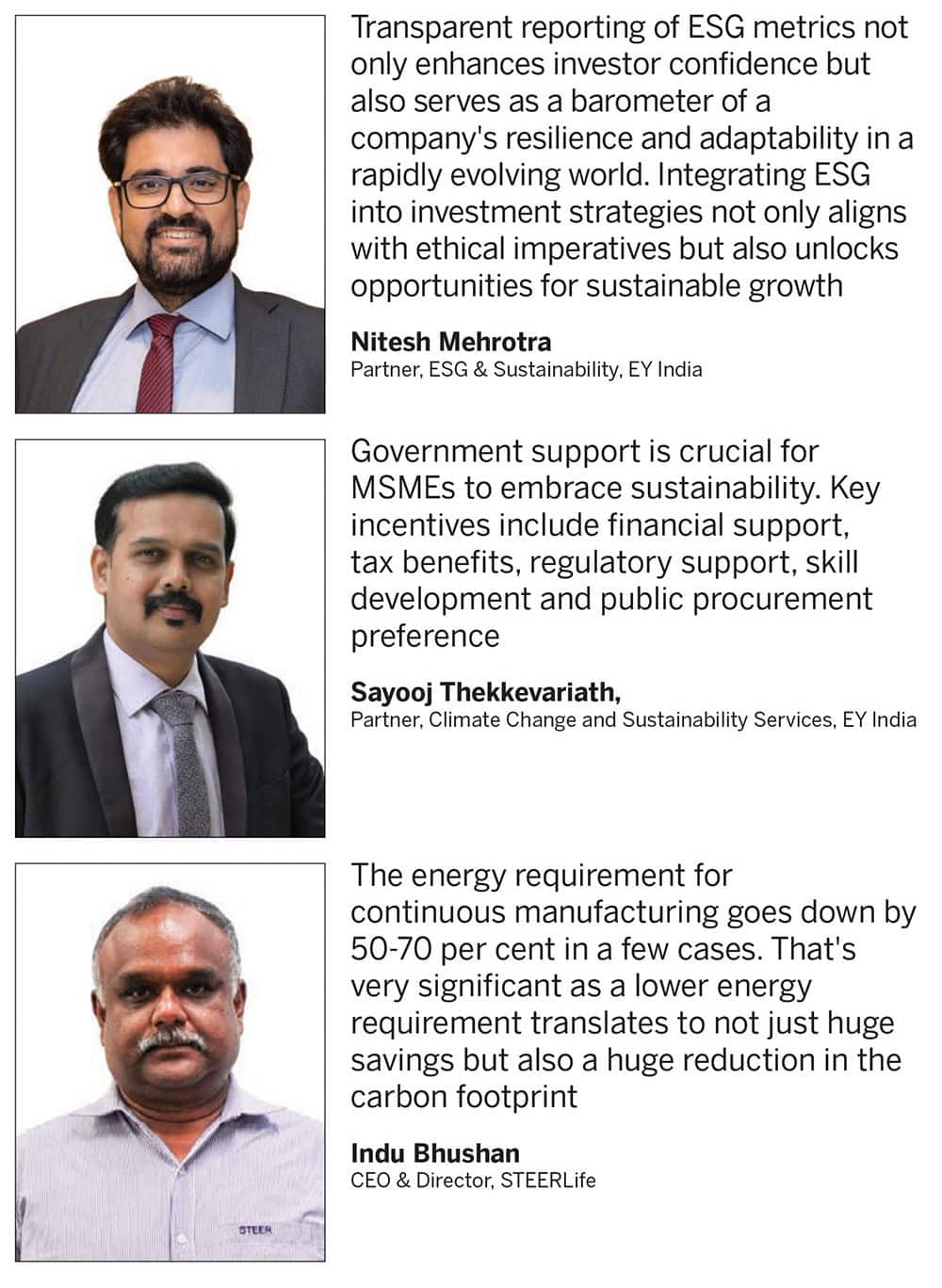
To put the cost pressures into perspective, Indu Bhushan says that with products like metformin, paracetamol, and ibuprofen, which are typically manufactured in tons every day, there is a significant energy cost involved. However, while these active pharma ingredients (APIs) are pretty cheap, there is a significant contribution from conversion cost.
For instance, according to him, a certain amount of API is lost as dust in the manufacturing process. Even if 0.5 per cent is the dust or the material lost in the cleaning process, different kinds of effluent treatments need to be done, adding to the cost.
So how does continuous manufacturing prove to be more sustainable than traditional batch manufacturing?
For one, Indu Bhushan estimates that the energy requirement for continuous manufacturing goes down by 50-70 per cent in a few cases. That’s very significant as a lower energy requirement translates to not just huge savings but also a huge reduction in the carbon footprint, reasons Bhushan. Listing the other advantages, according to Bhushan, continuous manufacturing also generates less effluents than batch processes, where multiple steps and a larger processing surface area translate to cleaning equipment and effluent treatment costs at every part of the process. These costs are reduced in continuous manufacturing systems.
Continuous manufacturing systems have a smaller footprint and therefore need smaller clean room facilities, further cutting down on energy and other utility requirements. As continuous systems are also automated, there is less chances of human error and therefore less reliance on quality control (QC) as most responses are measured online. And therefore, QC testing, which typically follows every step of the batch process, is not applicable in contiguous manufacturing, reasons Indu Bhushan.
He estimates that the gains would be greater when companies use continuous manufacturing right from the R&D and development stage, going to full-scale commercial manufacturing at a smaller scale.
As he reasons, “Lots of materials are saved during the development (phase) because whatever experience we gain, we (apply) it directly to the commercial scale. In fact, in the initial years of adoption, companies have used R&D scale equipment even for commercial scale without involving any scale-up or tech transfer. That not only reduces carbon footprint, but the go-to-market time also significantly reduces because you have all necessary data at one scale. And we are talking about various options available for a scale-up or increasing the batch size.”
On the time to get RoI, Indu Bhushan estimates that it takes between one and a half to two years for a manufacturer to get RoI on continuous manufacturing. Summing up, he mentions that apart from RoI, continuous manufacturing offers better flexibility in terms of batch size, and reduction in energy and effluents leading to better overall sustainability.
…but also more expensive
Indu Bhushan admits that continuous manufacturing is best applied to large volumes, with systems capable of producing 150-200 kg of material per hour, with STEERLife also providing very large commercial scale equipment producing 500 kgs to custom designing a system for one ton per hour line for a client. These systems are typically integrated and require expensive components, like gravimetric feeding and PAT tools, which are required for measuring loss on drying or content or uniformity from time to time. And that makes it more expensive than a batch processor.
Due to the high costs, he has observed two significant differences between how India and the West started adopting continuous manufacturing. Firstly, in the evolution from batch to continuous manufacturing, while the West is working on end-to-end continuous manufacturing, India’s pharma companies are at a hybrid stage where continuous manufacturing and automation are currently being deployed for stages which are more prone to human error.
Secondly, Indu Bhushan refers to collaborations between equipment manufacturers and contract development and manufacturing organisations (CDMOs) in the US. For example, GEA has collaborated with Hovione for continuous manufacturing of solid orals (continuous tableting). According to him, similar collaborations should happen in India because companies like STEERLife are not just equipment manufacturers, but also provide process solutions, enabling CDMOs which adopt continuous manufacturing to serve global clients.
A green government push
IPA’s Jain recommends that to further incentivise the sector, the government should introduce green subsidies, tax breaks, and low-interest loans for eco-friendly technologies. He believes that this will contribute to sustainable performance from a long-term perspective. Given the financial constraints faced by MSME pharma companies, Thekkevariath also agrees that government support is crucial for MSMEs to embrace sustainability. Key incentives include financial support (like subsidies, grants, and low-interest loans for green technology adoption), tax benefits (tax breaks for investments in sustainable practices and R&D), regulatory support in terms of simplified regulatory processes for environmental compliance and green projects, skill development involving investing in training programmes to build a skilled workforce for sustainable operations and finally, public procurement preference, which involves giving preference to environmentally friendly products in government procurement.
OPPI’s Matai points out that the recently announced Revamped Pharmaceuticals Technology Upgradation Assistance (RPTUAS) Scheme is a significant step in the government’s efforts to help upgrade the technological capabilities of our pharma industry and ensure its alignment with global standards. Eligibility for the PTUAS has been expanded beyond MSMEs to include any pharma manufacturing unit with a turnover of less than Rs 500 crores that requires technology and quality upgradation.
Sunil Kumar also emphasises that policy incentives can help offset the costs associated with compliance and make sustainability upgrades more financially feasible for MSME pharma companies.
Light at the end of the tunnel?
Given the challenges, Mehrotra from EY India reminds us that the path towards sustainability is not a sprint but a marathon, demanding unwavering commitment and resilience. He believes that by embedding ESG principles into their DNA, Indian pharma can not only mitigate risks but also drive innovation and foster societal well-being. As he puts it, “The green pill beckons and the time to heed its call is now,” referring to R&D efforts that are yielding breakthroughs in sustainable drug delivery systems and biodegradable packaging.
Going forward, Lupin’s Swaminathan projects that the company is aspiring to build a ‘Transformational Journey in Sustainability’. “Our focus is to empower employees to drive sustainability not only by metrics or setting ESG goals; we are looking at fostering a sense of purpose, community, and urgency. We believe by creating a culture that supports sustainability, organisations can unlock the full potential of their workforce and make a lasting impact on the planet.”
Shivshankar believes that the industry is moving in the right direction, with visible gains already being seen. “We must continue to work collectively to achieve this goal (of reducing overall carbon footprint), ensuring clear communication and complete transparency” is his call to action. Summarising the many benefits of embracing sustainable practices across production, R&D and supply chains, SIPL’s Sunil Kumar says, “In my opinion, those companies that proactively addressed sustainability and regulatory requirements were better positioned to comply with evolving regulations and avoid potential fines or operational disruptions.”
Thus while larger pharma companies are well on the sustainability path, mid-size and smaller companies can leapfrog early teething problems by exploring the learnings from these front-runners. Adapting and adopting best practices will need to become an urgent imperative to make sustainability part of their strategic growth plans.
The post appeared first on .